Advanced Welding WPS: Customizing Specs for Facility Projects
Grasping Welding WPS Requirements: Finest Practices and Techniques for Quality Welds
In the realm of welding, mastering Welding Procedure Specification (WPS) requirements is a critical component that directly affects the quality and stability of welds. Abiding by these standards makes sure consistency and integrity in welding outcomes. However, accomplishing quality in welds surpasses merely comprehending the requirements; it includes implementing best techniques and techniques that boost the craft to a level of accuracy and ability that sets apart the average from the outstanding. As we browse through the intricacies of welding WPS requirements, uncovering essential insights and methods for accomplishing top-tier welds will certainly be extremely important for welders seeking to excel in their craft and produce welds that stand the examination of time.
Recognizing Welding WPS Criteria

Understanding WPS standards is important for inspectors, engineers, and welders included in welding operations. By following WPS guidelines, welders can produce welds that fulfill the required mechanical homes and architectural honesty. Inspectors count on WPS documentation to verify that welding procedures are being adhered to properly which the resulting welds are of excellent quality. Designers utilize WPS standards to design welding procedures that make sure the durability and reliability of bonded structures.
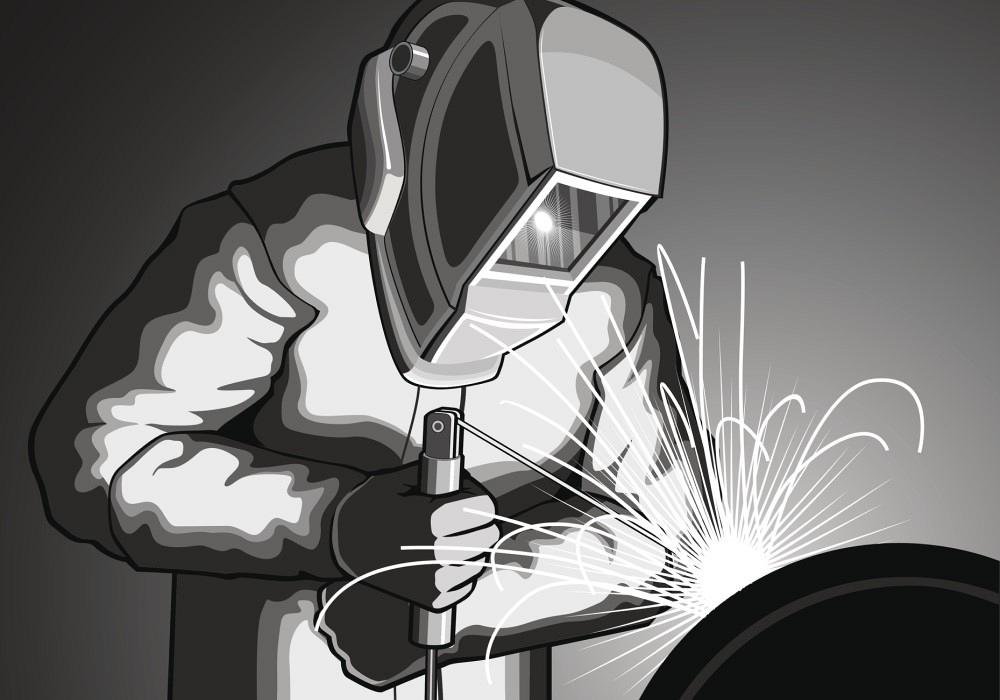

Necessary Devices for Quality Welds
Understanding welding WPS criteria is important for welders to effectively use the crucial devices needed for creating quality welds. The type of welding machine needed depends on the welding procedure being utilized, such as MIG, TIG, or stick welding. Cord brushes and cracking hammers are necessary for cleaning the weld joint before and after welding to remove any kind of contaminations that might influence the top quality of the weld.
Key Methods for Welding Success
To accomplish welding success, one have to understand the essential strategies important for creating top notch welds. One crucial strategy is keeping the appropriate arc size. Keeping the electrode at the optimum range from the workpiece is vital for developing solid, uniform welds. In addition, controlling the traveling speed is critical. Relocating also rapidly can cause not enough penetration, while relocating too gradually can bring about extreme warm input and possible flaws. Correct control of the electrode angle is one more vital technique. The angle at which the electrode is held can influence the bead form and infiltration of the weld. Moreover, ensuring consistent weapon angle and direction of travel is vital for uniformity in the weld bead. Finally, maintaining a secure welding and a constant hand setting throughout the procedure is key to achieving accuracy and consistency in the welds. By understanding these key strategies, welders can raise the quality of their job and attain welding success.
Ensuring Compliance With WPS Standards
In addition, preserving detailed records of welding criteria, equipment calibration, and assessment results is important for showing compliance with WPS standards. By diligently sticking to WPS requirements, welders can make sure that their work meets the needed quality levels and adds to the general success of the welding task.
Troubleshooting Common Welding Issues
When confronted with common welding problems, identifying the origin cause is essential for effective troubleshooting. One prevalent problem is the presence of porosity in welds, usually triggered by impurities such as dampness, oil, or corrosion. To resolve this, ensuring appropriate cleansing of the base metal before welding and using the correct he said securing gas can dramatically reduce porosity. An additional problem frequently come across is absence of blend, where the weld falls short to correctly bond with the base product. This can come from poor heat input or inappropriate welding strategy. Readjusting specifications such as voltage, wire feed rate, or travel speed can assist enhance combination. Additionally, distortion, splitting, and spatter prevail welding difficulties that can be mitigated via appropriate joint prep work, regular heat control, and picking the ideal welding consumables. By completely recognizing these typical welding problems check my blog and their origin, welders can effectively troubleshoot problems and attain high-grade welds.
Final Thought
Finally, mastering welding WPS criteria requires a complete understanding of the standards, making use of crucial tools, and carrying out crucial techniques for effective welds. Making sure compliance with WPS requirements is important for generating top quality welds and avoiding usual welding concerns. By adhering to ideal methods and practices, welders can achieve reliable and consistent results in their welding tasks.
In the world of welding, mastering Welding Procedure Requirements (WPS) criteria is a crucial part that directly influences the top quality and stability of welds.When delving right into the world of welding methods, a critical aspect to comprehend is the value and ins and outs of Welding Procedure Spec (WPS) criteria. WPS standards provide an in-depth standard for welding procedures, guaranteeing uniformity, top quality, and safety in the welding process. The type of welding machine required depends on the welding procedure being used, such as MIG, TIG, or stick welding.Achieving welding success with the mastery of crucial strategies demands a detailed understanding and adherence to Welding Procedure Requirements (WPS) standards.